High Grade Shallow Resource to Unlock Value at Burns Central
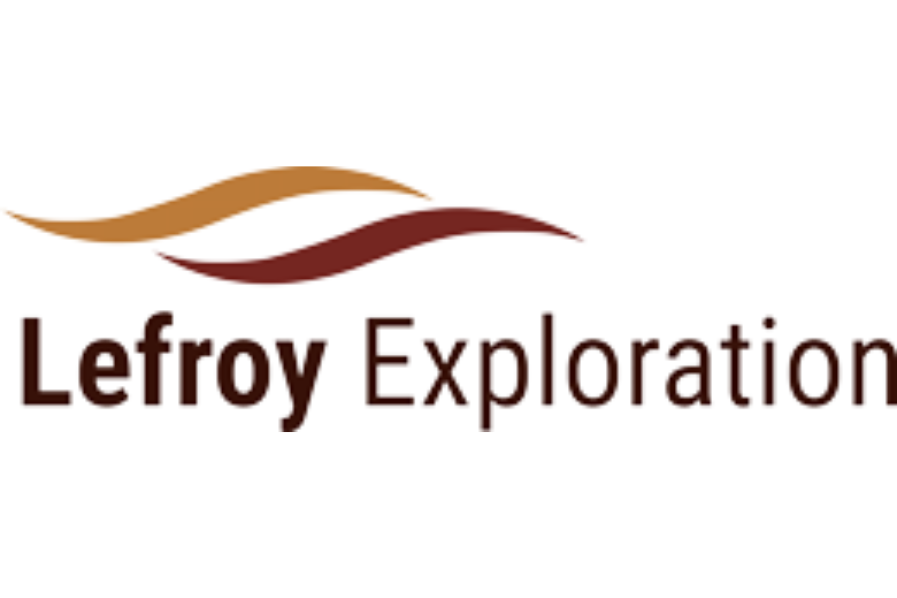
From trucks and drills to conveyors and crushers, mining equipment is subject to constant wear and tear. Traditionally, manual inspections have been the standard, but these are time-consuming, prone to human error, and offer limited real-time insight. Enter Artificial Intelligence (AI)—a game-changer for enhancing safety inspections across mining operations.
Enhancing Paperless Mining Equipment Inspections with AI
AI is transforming the way safety inspections are conducted in mining, allowing operators to not only streamline processes but also improve accuracy and safety.
Here’s how AI is reshaping mining safety:
1. Image Analysis and Defect Detection
AI-powered image recognition can analyse high-resolution images of mining equipment such as haul trucks, excavators, and drills to detect cracks, corrosion, leaks, and other mechanical defects that may be overlooked by human inspectors. This technology enhances the accuracy and consistency of inspections, particularly in rugged and hazardous environments where frequent manual checks are difficult.
2. Predictive Maintenance
By analysing historical data from previous equipment inspections, AI can predict when machinery components are likely to fail. This predictive maintenance model reduces unexpected downtime and ensures that critical mining equipment operates smoothly. It also allows companies to schedule repairs before a major failure occurs, thereby enhancing the overall safety and productivity of the mine.
3. Real-Time Monitoring
AI can integrate with IoT (Internet of Things) sensors on mining equipment to provide real-time data on various performance metrics, such as engine temperature, hydraulic pressure, and machine load. By analysing this data, AI can detect anomalies early, helping to prevent breakdowns and accidents that can jeopardize worker safety.
4. Automated Reporting
AI can generate detailed and automated inspection reports, complete with images of any detected issues, suggested corrective actions, and compliance notes. This not only saves time but also eliminates the risk of human error in documentation, ensuring that safety protocols are accurately followed and tracked.
5. Risk Assessment
AI evaluates multiple factors, such as equipment usage patterns, age, wear and tear, and operating conditions, to generate risk scores for individual pieces of machinery. This helps prioritize maintenance efforts on the most vulnerable equipment, ensuring resources are allocated effectively to maintain a safe working environment.
6. Compliance Management
Mining operations must adhere to strict safety regulations and industry standards (e.g., MSHA, ISO). AI helps automate compliance checks and generates comprehensive, audit-ready reports that ensure your mining equipment meets all safety standards without the need for manual verification.
Benefits of AI-Enhanced Mining Equipment Inspections
1. Improved Safety
By identifying potential equipment failures early, AI helps reduce the risk of accidents that could endanger miners and cause costly operational delays. This proactive approach to safety ensures that any machinery defects are addressed promptly, safeguarding the well-being of workers in hazardous environments.
2. Increased Efficiency
Automating data collection, analysis, and reporting streamlines the inspection process, freeing up operators and safety personnel to focus on other critical tasks. With AI, mining operations can maintain optimal safety levels while simultaneously improving operational efficiency.
3. Enhanced Decision-Making
AI provides real-time insights and predictive analytics, allowing for more informed decisions about equipment maintenance and safety protocols. Mining operators can rely on AI data to schedule repairs or replacements, reducing downtime and improving the longevity of equipment.
4. Better Compliance
Ensuring compliance with mining safety regulations is a time-consuming task, but AI makes it easier by automating checks and generating reports that can be readily shared with regulatory bodies. This reduces the administrative burden on safety managers while ensuring all machinery complies with necessary standards.
5. Cost Reduction
Mining operations can see significant cost savings by reducing downtime, minimizing the risk of accidents, and optimizing maintenance schedules. With AI-driven inspections, mines can avoid costly repairs, equipment replacements, and regulatory fines.
Challenges and Considerations
While AI offers numerous advantages for mining equipment inspections, it is not intended to fully replace human inspectors. Challenges such as data quality, algorithm bias, and cybersecurity concerns need to be addressed. Additionally, a skilled workforce is necessary to oversee the implementation and management of AI technologies within mining operations.
Conclusion
By adopting AI, the mining industry can elevate safety standards, protect workers, and ensure equipment reliability. The future of mining safety inspections lies in the intelligent collaboration between cutting-edge technology and human expertise. This partnership between AI and human oversight can lead to safer, more efficient, and cost-effective mining operations.
Hear more from
Naaman Shibi
Paperless Solutions Expert
Pervidi Paperless Solutions
Source
Comments are closed.