Broad High Grade Lithium Intersections Extend BP33
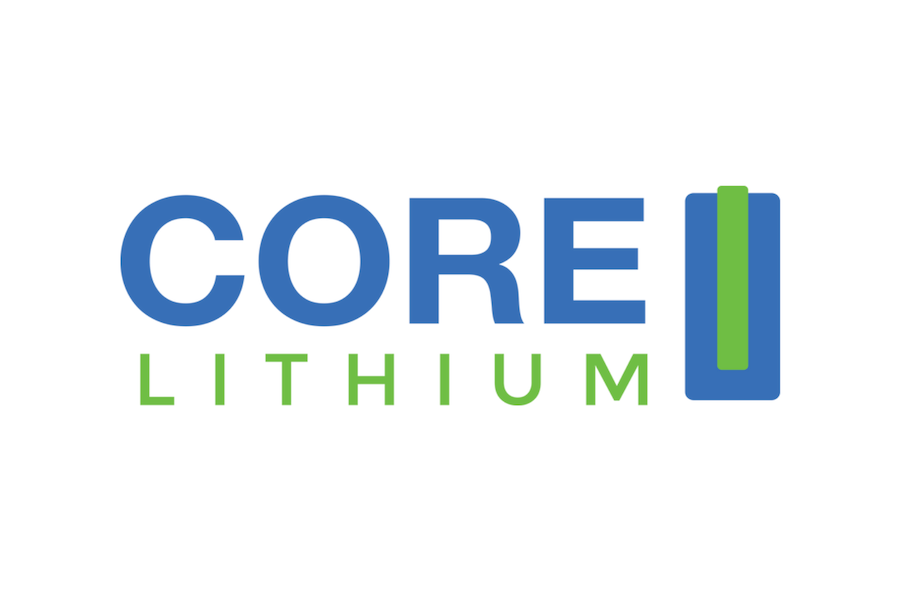
Utilizing proprietary technologies, Gradiant’s goal is to reduce water use, minimize wastewater discharge, reclaim resources and convert wastewater into freshwater. To better serve the lithium sector, the company recently spun out alkaLi, a new company focused on scaling battery-grade lithium production using its proprietary EC2 technology.
As noted on the company’s website, EC2 is designed to extract, concentrate and convert lithium quickly and efficiently, reducing operational costs and environmental impact. The technology, which adapts to various lithium sources and integrates with existing infrastructure, has been successfully tested and proven commercially.
“It’s a startup that benefits from over a decade of experience, and from all the funding we have raised,” said Bajpayee.
For Govindan, Gradiant’s success in the water treatment space is a natural fit for the lithium extraction sector.
“The DLE space is glorified water treatment,” he explained while speaking with INN. “Adsorption, resins, ion exchange and membranes are our bread-and-butter water treatment processes. “
Gradiant’s primary water focus and proprietary technologies give alkaLi an edge, noted Bajpayee.
“I think one difference is we are a water company trying to do DLE, not a DLE company trying to do water. Because you can’t just do DLE — you either have to do water, or you have to partner with water companies,” the CEO explained.
alkaLi’s EC2 is a flexible, three stage system designed to process lithium from various sources, including brine, evaporation and recycling. It can be used in full or in standalone stages, integrates with existing infrastructure and offers an option to boost production with Gradiant’s SmartOps AI platform.
Extracting value from wastewater
While alkaLi is lithium centric, Gradiant has a long history of aiding the mining sector in the extraction of commodities from water. “We have worked across mining applications, not just critical minerals like nickel, cobalt and lithium, but also iron ore mines, uranium mines and other sectors,” said Govindan.
In his view, the mining sector has two very specific issues. First, in lithium processing, the mineral is found in water, requiring expertise in concentration, decontamination and conversion to produce battery-grade materials. This process is also applicable to nickel, cobalt and other critical minerals.
The second issue is wastewater treatment or tailings reprocessing, such as in Chile’s copper mines, where tailing ponds contain critical minerals and highly polluting wastewater. The technology Gradiant has developed can reclaim valuable minerals while recycling wastewater into fresh water for industrial use.
Pointing to Chile’s Atacama province, where water scarcity is a prominent issue, Govindan noted that as much as 60 percent of the potable water in the region is used for mining applications.
“When we recover and reuse that wastewater to the extent of 90 percent, we can reduce that 60 percent all the way down to 6 percent,” he said. “So it’s a huge environmental impact, water sustainability impact.”
According to a 2023 article published in the journal “Science of the Total Environment,” tailings reprocessing can reduce the amount of tailings that need to be stored, minimize the greenhouse gas emissions associated with new mining and supply approximately 2 percent of the EU’s future copper demand.
Govindan highlighted a nickel project in Australia, where the company was brought in to recover 20 percent of the nickel that wasn’t recovered during processing, leading to losses in wastewater.
Gradiant proposed a solution to recover much of the lost nickel, significantly boosting the project’s profitability.
Targeting tailings can also produce industrial water for reuse, as the Gradiant executives pointed out. Additionally, as Bajpayee noted, the processes used by Gradiant and alkaLi not only produce reusable water, but can also recover salt and other minerals, resulting in “true zero-discharge projects.”
Junior-focused business model
Being able to recover lost minerals while reusing water can lead to significant cost savings.
“Instead of selling the equipment and walking away, we will put it at the site and operate the equipment. The owner pays us per liter of water we produce, per tonne of lithium we produce, which really helps the juniors,” said Govindan.
“(Juniors) are in a capital-intensive industry, and when prices are US$12,000 per tonne for lithium, they’re not able to raise capital. Then there is Gradiant, the only unicorn in the water tech space. We have an excellent balance sheet; also we are able to raise debt and equity capital, which we can use to help them by putting the equipment ourselves.”
EC2’s modular design makes it easy and fast to set up, which is another plus for junior miners looking to take advantage of future market trends quickly. “Two things are very important in terms of product philosophy for us (and) for lithium especially: productization and digitalization. The EC2 technology is very modular and it’s very digital,” said Govindan.
“We have artificial intelligence; we have a SmartOps platform we developed for water treatment, but is lithium applicable. So we are able to provide highly modular, highly digitalized solutions.”
For companies looking to produce lithium hydroxide instead of carbonate, a simple converter can be implemented that converts carbonate to hydroxide, the executives explained.
Being a bespoke water-first company also makes the technologies developed by Gradiant versatile.
“Using variable brines is something that actually comes quite naturally to us,” said Bajpayee. “And the ability to customize solutions makes it also widely applicable, whether it’s South America, the US or Australia.”
Aside from designing water solutions for industries like mining, Gradiant has developed technologies to target perfluoroalkyl and polyfluoroalkyl substances (PFAS), also known as forever chemicals.
Gradiant’s ForeverGone is a comprehensive solution for permanently eliminating PFAS. Unlike current technologies that only transfer PFAS waste, ForeverGone uses micro-foam fractionation to concentrate PFAS, as well as a destruction engine for electro-oxidation to completely destroy the chemicals.
This process ensures water meets or exceeds US Environmental Protection Agency standards, offering an efficient, cost-effective and sustainable method for PFAS removal.
“(The goal is) to build an impact that will outlast you. That’s the ultimate measure of success,” said Bajpayee.
Don’t forget to follow us @INN_Resource for real-time news updates!
Securities Disclosure: I, Georgia Williams, hold no direct investment interest in any company mentioned in this article.
Editorial Disclosure: The Investing News Network does not guarantee the accuracy or thoroughness of the information reported in the interviews it conducts. The opinions expressed in these interviews do not reflect the opinions of the Investing News Network and do not constitute investment advice. All readers are encouraged to perform their own due diligence.
Comments are closed.